All the electronic products have to use PCB to function, so there is a consensus that the trend of PCB market almost indicates the dynamic of the electronic industry. With the development of phone, laptop and PDA and the other advanced, small-sized electronic products like the wearable devices, the demands for flexible printed circuit boards are increasingly growing.
PCB manufacturers are focused to create thinner, lighter and higher-density FPC to seize this thriving market.
Under the background, I consider it necessary to write about the differences between single-sided flex PCB, double-sided flex PCB and multilayer flex PCB, whether for the PCB fabricators or the open source hardware makers who are likely to
buy flex PCB, this will be a useful and inspiring article about flexible PCB.
1. Single-sided flexible printed circuit board
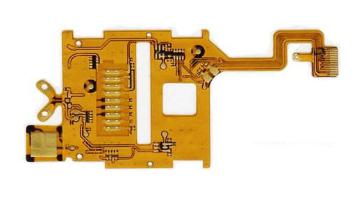
Single-sided FPC has a layer of chemically etched conductive pattern, and the conductive pattern layer on the surface of the flexible insulating substrate is a rolled copper foil. The insulating substrate could be aramid fiber, polyethylene terephthalate, polyimide and polyvinyl chloride. Single-layer flexible PCB can be divided into the following four sub-categories:
1). Single-sided connection without covering layer
The conductive pattern is on the insulating substrate, the surface of leads is without covering layer, they are interconnected by soldering, welding or pressure welding. This FPC is commonly used in the early telephone.
2). Single-sided connection with covering layer
Comparing to the above FPC, this kind of FPC is with a covering layer on the surface of the lead. What is worth noting is, the pads need to be exposed when covering, the terminal area could be free of covering if permits. This kind of single-sided FPC is the most widely used and normally applied to automotive instrumentation, electronic equipment.
3). Double-sided connection without covering layer
The connecting pad could be connectable whether on the front side or back side of the lead. A via hole is formed on the insulating substrate around the pad by stamping, etching or other mechanical methods.
4). Double-sided connection with covering layer
Unlike the last type of double-sided FPC, the surface of this type of FPC has a covering layer with vias that allow it to be terminated on both sides and still retain the covering layer, it is made of two layers of insulating material and a layer of metal conductor.
2. Double-sided flexible printed circuit board
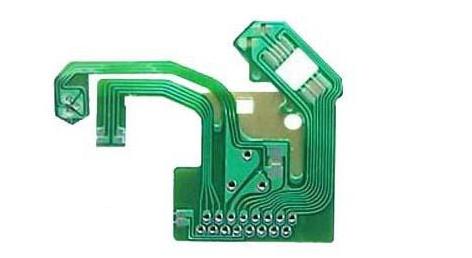
Double-sided flex PCB has a layer of etched-made conductive pattern on both sides of the insulating base film, this increases the wiring density per unit area. The metallized holes connect the patterns on both sides of the insulating material to form the conductive paths to meet the design and functions of the flexibility. The cover film can protect the single-sided and double-sided leads and indicates where the components are to be placed. Depending on requirements, metallized holes and covering layer are optional. There are fewer applications for this type of FPC.
3. Multilayer flexible printed circuit board
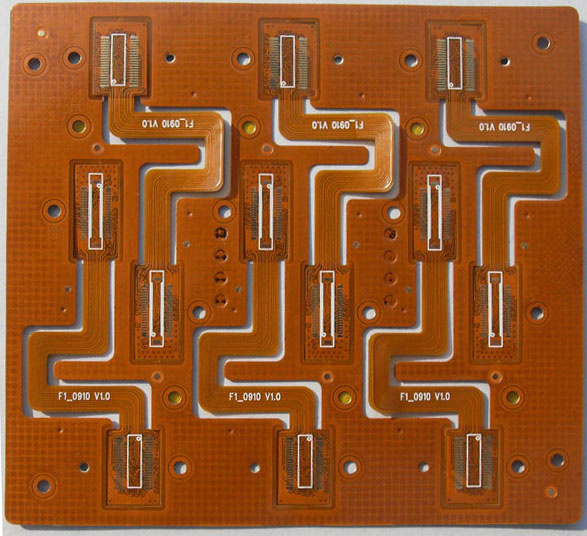
Multi-layer flex PCB laminates three or more layers single-sided or double-sided flexible circuits together, and make metallized holes by drilling and plating so as to form the conductive pathway between different layers. This eliminates the need for complex welding processes. Multilayer circuits have huge functional differences in terms of higher reliability, better thermal conductivity, and easier assembly performance.
The advantage of multilayer FPC is the substrate film is lightweight and has excellent electrical properties, such as the low dielectric constant. Multilayer flex PCB made from polyimide film is about 1/3 lighter than multi-layer PCB with rigid epoxy glass cloth, but it lost the flexibility of single side and double side flexible PCB. Multi-layer FPC can be further divided into the following types:
1). Flexible insulation substrate finished products
This category multilayer FPC is made based on the flexible insulating substrate, the finished product is defined as being flexible. This construction typically bonds both ends of many single-sided or double-sided, micro-flexible PCBs but without the central portions being bonded to provide a high flexibility. Furthermore, in order to be highly flexible, a thin, suitable coating, such as polyimide, could be used on the lead layer instead of a thicker laminate overcoat.
2). Soft insulating substrate finished products
This category flexible PCB is made on the basis of the soft insulating substrate. The finished product is not required to be flexible. This type of multi-layer FPC is made by laminating using a soft insulating material, such as a polyimide film, which lost the flexibility after lamination.