1. The overlap of the welding plates.
a. The overlap of welding plates means the holes are overlapped, when multiple drilling happens to one position, it would result in the damage of hole.
b. Overlap of two holes in a multi-layer board will cause it scrapped.
2. The abuse of graphics layer.
a. Doing some useless connection in the graphics layer is easily misunderstood, for example, a design for
4 layer PCB uses the circuit of 5 layer PCB or even above.
b. In violation of conventional design, such as, the side of electronic parts is designed at the Bottom layer, and the welding side is designed at the Top layer, these all will cause troubles.
3. The characters are in a mess.
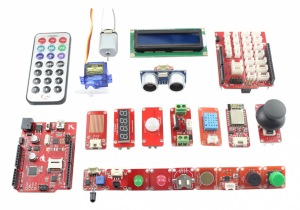
a. Too small characters will increase the difficulty of silk-screen printing, too large characters will make them overlapped with each other and hard to tell.
4. Setting of single-sided welding plate aperture.
a. There is normally no need to drill for single-sided welding plate, in the case of drilling being needed, it’s supposed to mark the location and design the aperture to be zero, this is because there will be a coordinate occurring at the location when drilling numbers are generated, which easily cause problems.
b. For the single-sided welding plate, it should be marked when drilling.
5. Draw the welding plate with filling stuff.
Drawing the welding plate with filling stuff is not workable for processing even though it can pass the DRC test, because the welding plate is not able to directly generate the solder mask, when adding the solder mask, the filling stuff area will be covered by solder mask, this could bring troubles to welding components.
6. Electric stratigraphy is with Thermal Pad and also
For the power supply that is designed as the Thermal Pad, stratigraphy is opposite to the image on the actual printed circuit board, and all the lines are shielded lines, this should be very clear for designers. Also importantly, designers should be very careful with drawing the shielded lines, any gap or breach is not allowed because it will cause short circuit.
7. Unclear definition of processing layers
a. Single-sided board is designed at the Top layer, if do it on the front side and back side without any instruction, it’s likely that the finished board would be hard to do welding.
b. If a 4 layer PCB is designed to be in the order of Top mid1 and mid2 bottom, this needs to mark and explain, or it will not be in the same order when processing.
8. There is too much filling stuff or filling stuff is filled with extremely thin lines.
a. There is a loss in the light painting data.
9. Surface mount components pads are too short
This is for the on-off test. For the high-dense surface-mount components, the spacing between their feet is quite small, the pad is also quite fine, the installation of test pins must stagger the position up and down(left and right). If the pads are too short, they don’t affect the installation of components, but could make the test pin hard to work.
10. Large copper foil is too close to the frame.
Large copper foil should be 0.2mm far away from the frame at least. Because in the milling shape, milling to the copper foil is likely to cause the copper foil lift and the detachment of solder resist.
11. Unclear design of frame
Some customers design the contour line in the Keep layer, Board layer, Top over layer and these lines do not overlap, this will make
pcb manufacturers difficult to determine which contour line is the main one.
12. graphic design is not uniform.
Uneven coating is caused in the process of graphics plating, this will affect the quality.
13. Grid lines should be used when the area of copper layer is too large, which is to avoid bubble when doing SMT.